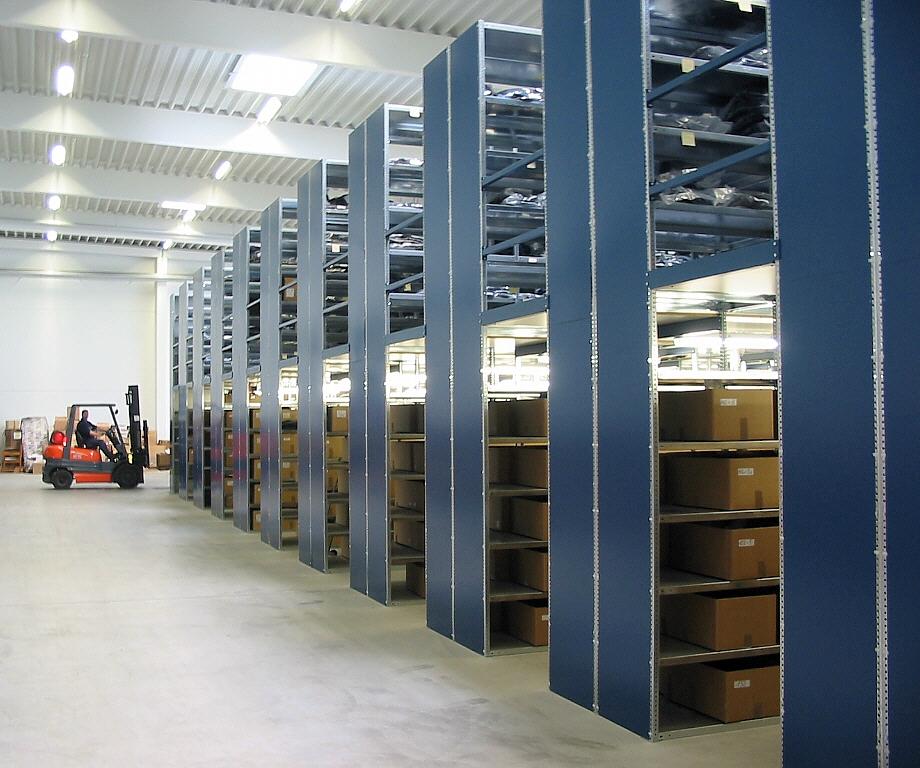
STORAGE
DIN 7716 (Guideline for the Storage, Maintenance and Cleaning of Rubber Products) applies to the storage of O-rings. It is important to store it properly. The service life of O-rings can be affected by many influences, such as light, heat, humidity, oxygen, ozone, etc. and thus changed. The ideal temperature for storage is between +5 and +20 degrees °C. In general, storage sealed in polyethylene bags is considered optimal. We recommend that you do not significantly exceed the following storage times:
NBR | HNBR | EPDM | FKM | VMQ |
---|---|---|---|---|
4 years | 4 years | 6 years | 10 years | 10 years |
VALID RANGE
The following guidelines (excerpt from DIN 7716) apply to rubber products in pure form and in combination with other materials, namely to elastomers made of natural rubber and/or synthetic rubber, as well as to adhesives and solutions. The guidelines according to DIN 7716 sections 3 and 4 are primarily requirements for long-term storage (generally longer than 6 months). For short-term storage (less than 6 months) – such as in production and distribution warehouses with continuous material outflow – the provisions of DIN 7716 are applicable mutatis mutandis, except for the general requirements for storage space according to sections 3 and 3.1, as long as the appearance and function of the products do not undergo any adverse changes (see DIN 7716 section 2) and as long as there is no contradiction with special requirements of this standard for expressly short storage periods of rubber products (see DIN 7716 section 4.2.b)
GENERAL
Under unfavourable storage conditions or improper handling, most rubber products change their physical properties. They can become unusable, for example, due to excessive hardening, softening, permanent deformation, as well as flaking, cracking or other surface damage. The changes can be caused by exposure to e.g. oxygen, ozone, heat, light, moisture, solvents or storage under voltage. Properly stored and treated rubber products remain almost unchanged in their properties over a long period of time (a few years).
STORAGE
The storage room should be cool, dry, dust-free and moderately ventilated.
TEMPERATURE
The storage temperature should be +15 °C and must not exceed +25 °C, otherwise the physical properties may harden or the service life may be shortened. The storage temperature should also not be below -10°C. Lower temperatures are generally not harmful to rubber products, but they can become very stiff at lower temperatures. Highly cooled products must be brought to a temperature of over +20 °C for a long time before commissioning. Adhesives and solutions must not be stored colder than 0 °C, and rubber products made of certain types of chloroprene rubber may not be stored colder than +12 °C.
HEATING
When heating the storage room, radiators and pipes must be screened. The heat sources in the storage rooms should be designed so that the distance between the radiator and the stored goods is at least 1 m.
HUMIDITY
Rubber products should not be stored in damp storage rooms. Care must be taken to avoid condensation. The relative humidity is best below 65%.
LIGHTING
The rubber products should be protected from light, in particular from direct sunlight and from strong artificial light with a high ultraviolet content. For this reason, the windows of the storerooms must be provided with a red or orange (under no circumstances blue) protective coating. All light sources emitting ultraviolet rays, such as openly installed fluorescent tubes, are particularly harmful because of the ozone formation associated with them. Room lighting with normal incandescent lamps is preferable.
OXYGEN/OZONE
The rubber products should be protected from air exchange, especially draughts, by wrapping, by storage in airtight containers or by other means. This refers mainly to articles with a large surface area in relation to the volume, e.g. rubberized fabrics or cellular articles. Since ozone is particularly harmful, the storage rooms must not contain any ozone-generating equipment, such as fluorescent light sources, mercury vapor lamps, electric motors or other devices that can produce sparks or other electrical discharges. Combustion gases and vapours, which can lead to ozone formation due to photochemical processes, should be eliminated. Solvents, fuels, lubricants, chemicals, acids, disinfectants, etc. must not be stored in the storage room. Rubber solutions must be stored in a special room in compliance with the official regulations on the storage and transport of flammable liquids.
DEFORMATION
Care must be taken to ensure that rubber products are stored stress-free, i.e. without tension, pressure or other deformations, as stresses promote both permanent deformation and cracking. Certain metals, especially copper and manganese, have a damaging effect on rubber products. For this reason, rubber products must not be stored in contact with these metals, but must be protected by packaging or by finishing with a layer, e.g. paper or polyethylene. The materials of the containers, packaging and covering material must not contain any components that are harmful to rubber products, e.g. copper or copper-containing alloys, petrol, oil and the like. Films containing plasticizers must not be used for packaging. If rubber products are powdered, the powder must not contain any components that are harmful to the rubber products. Talc, mud chalk, fine-grained mica powder and tear starch are suitable for powdering. Rubber products of different compositions must be avoided from touching each other. This is especially true for rubber products of various colours. Rubber products should remain in storage for as short a time as possible. In the case of long-term storage, care must be taken to ensure that new products are stored separately from those already available. At this point, we would like to draw your attention to the DIN 9088 Aerospace Guidelines for the permissible storage times of products made of elastomers.
CLEANING AND MAINTENANCE
Rubber products can be cleaned with soap and warm water. The cleaned items should be dried at room temperature. After a longer storage period (6 to 8 months), the products can be cleaned with a solution of 1.5% sodium carbonate. The residue of the cleaning liquid should be rinsed off with water. Effective and particularly gentle cleaning agents are recommended by the manufacturer. Solvents such as trichloroethylene, carbon tetrachloride and hydrocarbons must not be used for cleaning. Furthermore, the use of sharp-edged objects, wire brushes, sandpaper, etc. reproduced with the permission of the German Standards Committee is prohibited for this purpose. The latest edition of the standard sheet in A4 standard format, which is available from Beuth-Vertrieb GmbH, is decisive.