The main advantages of the elastomer / rubber O-ring are its low weight, its low space requirement, its high media and temperature resistance and its favourable price-performance ratio. The different types of O-ring seals are static and dynamic. Static sealing is a seal in which the coupling elements are not subject to any corresponding displacement. Dynamic sealing is a seal in which the coupling elements are in corresponding movement with each other.
O-rings
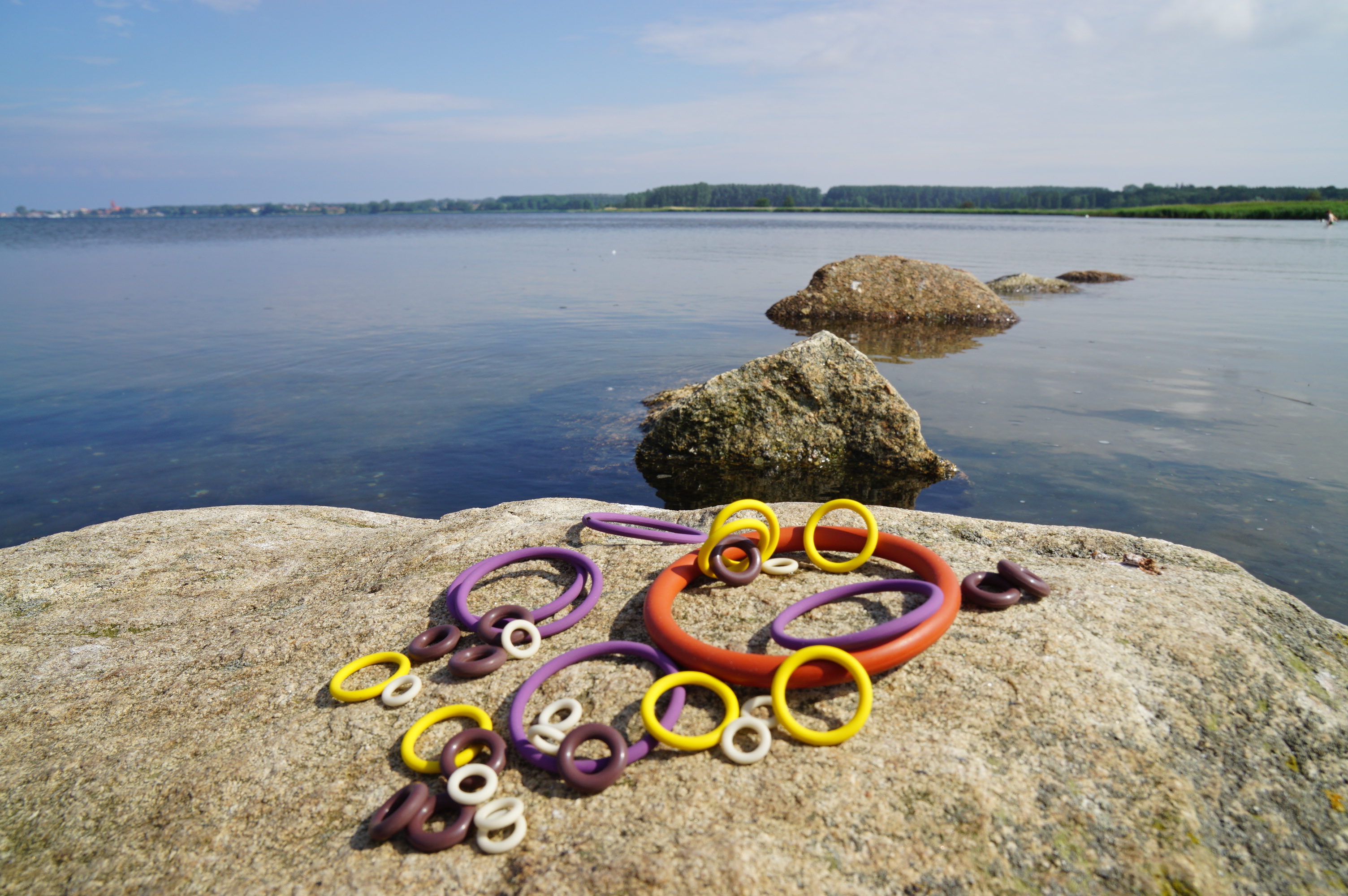
O-ringsCAN BE PRODUCED FROM THE FOLLOWING MATERIALS
Material ISO 1629 | Base Elastomer | Trade names Trademarks | Temperature insert (standard) |
---|---|---|---|
ACM | polyacrylate rubber | Nipol® | -20° to + 150° C |
AEM | ethylene acrylate rubber | Vamac® | -30° to + 150° C |
AU | polyester urethane | Adiprene® | -30° to + 90° C |
CR | chloroprene rubber | Neoprene® | -40° to + 100° C |
CSM | chlorosulphonyl polyethylene rubber | Hypalon® | -30° to + 120° C |
EPDM | ethylene-propylene-diene rubber | -40° to + 140° C | |
FEPM | Tetrafluoroethylene-propylene copolymer rubber | Aflas® | -30° to + 200° C |
FFKM | perfluor rubber | HPF | -15° to + 270° C |
FKM | fluorinated rubber | Viton® | -20° to + 200° C |
FVMQ | fluorosilicone rubber | Silastic® | -45° to + 175° C |
HNBR | Hydrogenated nitrile butadiene rubber | -15° to + 150° C | |
IIR | butyl rubber | Polysar Buthyl® | -40° to + 130° C |
NBR | nitrile butadiene rubber | -25° to + 100° C | |
PTFE | polytetrafluoroethylene | Teflon® | -200° to + 260° C |
SBR | styrene-butadiene rubber | Intol® | -40° to + 100° C |
VMQ | Methyl vinyl rubber / silicone | Siloprene® | -50° to + 210° C |
ACM
✔
Mineral oils, (engine, transmission and ATF oils), aging and ozone
×
Aromatic and chlorinated hydrocarbons, brake fluids, hot water, water vapor, acid and alkaline solutions
CR
✔
Water, aqueous solutions at low temperatures Refrigerant, aging and ozone
×
Aromatic hydrocarbons, esters ketones and glycols
EPDM
✔
Brake fluids, various acids and alkalis Hot water and steam, aging and ozone
×
Mineral oils and fats, natural gas, linoleic acid, ether, hexane, gasoil and freon 112
FFKM
✔
extremely high temperatures (air up to 270° C - special compounds up to 315° C) resistant to solvents and further 1600 media
×
Liquid oxygen, dichloroacetic acid
FKM
✔
high temperatures up to 200° C (medium air), mineral oils, vegetable and animal fats aromatic and chlorinated hydrocarbons, aging and ozone
×
Brake fluids, highly polar solvents, acetone, caustic potash, formic acid, acetic acid and chlorobenzene.
HNBR
✔
Vegetable and animal fats and oils, aliphatic hydrocarbons, water and steam up to 140° C, aging and ozone
×
chlorinated hydrocarbons, solvents, concentrated acids/alkalis
NBR
✔
Gasoline, mineral oils and greases, light heating oil, propane, butane, aliphatic hydrocarbons
×
Super fuels with high aromatic content, benzene, acetone, brake fluid, ozone.
PTFE
✔
almost all organic and inorganic chemicals (over 1800 media) high and low temperature application, weathering and aging
×
Alkali metals in molten or dissolved form, fluorine and fluorine compounds
VMQ
✔
high temperatures, hot air, oxygen, water, aging and ozone
×
Silicone oils and greases, fuels, exhaust gases
O-ringsQUALITY CRITERIA
The O-ring dimensions and standard qualities we keep in stock meet the requirements of DIN 3771 Part 1-5, grade characteristic N. DIN 3771 Part 4 defines the permissible shape and surface deviations of O-rings.
Permissible defect sizes are differentiated according to the variety characteristics N and S. Unless otherwise specified, O-rings will be supplied according to grade N. These meet the requirements for standard quality.
O-ringsTOOLS
Due to our own tool construction we have the possibility of a cost-effective and fast production of your O-ring dimensions with special tolerances from the desired or required material.
O-ringsSTORAGE
DIN 7716 (guidelines for storage, maintenance and cleaning of rubber products) applies to the storage of O-rings. Proper storage is important. The service life of O-rings can be affected by many influences, such as light, heat, humidity, oxygen, ozone, etc., and thus changed. The ideal temperature for storage is between +5 and +20 C. In general, storage in polyethylene bags welded together is considered optimal. We recommend not to exceed the following storage times significantly:
Generally recommended storage time of elastomers:
NBR | 4 years |
HNBR | 4 years |
FKM/FPM | 10 years |
VMQ | 10 years |
EPDM | 6 years |
CR | 4 years |
Viton®, Hypalon® and Teflon® are registered trademarks of DuPont Performance Elastomers.
The other trademarks and brand names are the property of their respective owners.